|
Formwork |
|
|
Permanent Formworks
|
|
Permanent
formworks are part of the permanent structure of the building.
The main advantages are that they save time and labour as there
is no need to dismantle the formwork. They reduce costs and save
time by (source: CIRIA C558): |
|
·
Reducing the skill level needed on site. |
·
Increasing the potential for
standardisation and repetition. |
·
Permitting off-site fabrication in factory
conditions followed by scheduled and
appropriate deliveries. |
·
Speeding up erection times, particularly in building works. |
·
Eliminating the need to strike formwork
and falsework. |
·
Allowing early access for following or concurrent operations. |
·
Eliminating the programme limitations of reuse of formwork. |
|
The use of permanent
formwork can reduce construction and maintenance costs, shorten
construction time,
and improve safety by reducing hazards during construction. It also
reduces construction
waste generation during construction.
Maintenance costs are
reduced by: |
·
Improving
curing of concrete and reducing shrinkage craking. |
·
Ensuring
adequate cover to the reinforcement and providing associated benefits
such
as
increased resistance to chloride ingress and carbonation, where appropriate. |
·
In many
instances improving the durability of the structure. |
·
Providing
the decorative finish required. |
|
Definitions |
Permanent
formwork is a structural element that is used to contain the placed
concrete, mould it to the required dimensions and remain in place for the
life of the structure.
Participating permanent formwork makes some predetermined contribution to
the strength of the structure.
Non-participating permanent formwork makes no strength contribution but may
provide additional benefits such as improved durability, finish or
insulation properties.
Potential
applications and benefits of permanent formwork (source: CIRIA C558): |
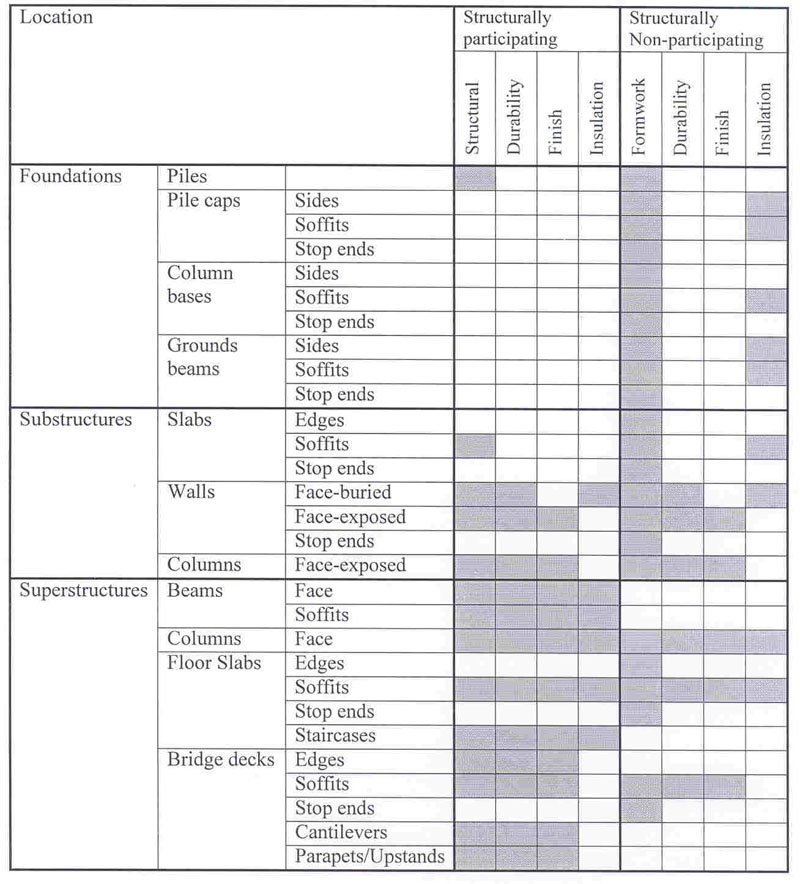 |
|
Checklist of
recommended applications of materials for permanent formwork |
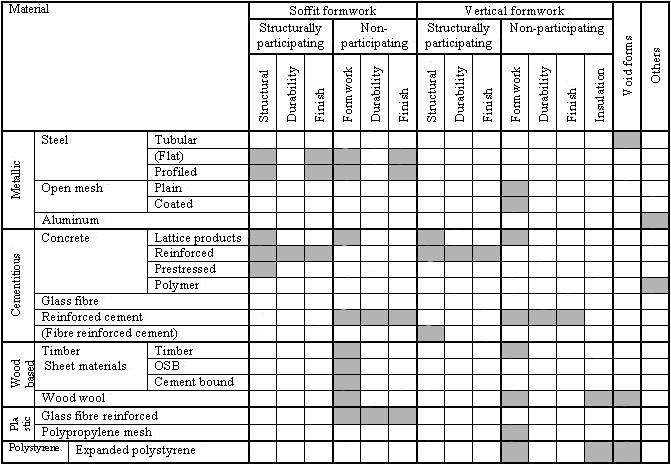 |
Description
of some permanent formwork. |
|
Examples in Hong Kong |
Concrete Permanent Formwork |
Semi-Precast slabs |
 |
The
Cambridge House, Quarry Bay. |
 |
The
Rosedale on the Park Hotel, Causeway Bay. |
|
Metal Permanent Formwork |
Staircases |
 |
The
Charter House, Central. |
|
|
![]() |
|
|
|
Steel mesh
|
Steel mesh can be used as permanent formwork, generally in vertical
applications, with either a small opening, similar to largest
aggregates size, to retain the placed concrete directly or as a
larger size mesh with additional coating. |
|
Common Usage as permanent formwork: |
 |
Construction joints in slabs. |
 |
Deep construction joints. |
 |
Vertical construction joints to walls. |
 |
Wall and column formwork, for further finishing or rendering. |
 |
Soffit formwork. |
 |
Curved wall formwork. |
 |
Arch formwork. |
|
Span Range: |
 |
At the
base of thick walls and deep stop ends supports at 225 to 325mm
centers, depending on thickness. |
 |
Shallow stop ends 675 to 725mm for 500mm slab depending upon
thickness. |
 |
For
soffit of 300mm slab supports at 425 to 575mm depending upon
thickness. |
|
|
Advantages: |
 |
Economies of cost and speed over traditional methods. |
 |
Light and easy to handle. |
 |
Easily cut and fitted to awkward shapes by unskilled labour. |
 |
Benefits can be taken of reduced formwork pressures when using
expanded mesh. |
 |
Pour can be monitored from partially exposed face. |
 |
Continuity of reinforcement through stop ends can readily be
accommodated. |
|
Disadvantages: |
 |
Produces an unformed face which is acceptable for stop ends to receive
further concrete but must be rendered/faced for a fair finish. |
|
CEMENTITIOUS |
|
|
Concrete |
Lattice products |
Precast concrete panels up to 2400mm wide reinforced by welded
lattices which project into, and provide a mechanical linkage with,
the in-situ concrete slab. |
|
|
Common usage :
|
 |
Composite concrete floors spanning between either steel or concrete
beams. |
 |
Composite bridge decks spanning between either steel or concrete
beams. |
|
Span Range : |
 |
Up
to approximately 3.8m for self-supporting units. |
 |
Larger spans, up to 10m, will require propping at construction stage. |
 |
Longer panels are available for particular applications. |
|
Advantages: |
 |
Lower cost and higher speed over traditional methods. |
 |
Large areas quickly placed with mechanical handling. |
 |
Large span range. |
 |
Compatible material. |
 |
Can
simplify reinforcement detailing, particularly when used in building
works. |
|
Disadvantages: |
 |
Relatively heavy, will require some mechanical handling. |
 |
Access difficult when in position, will require the provision of
access routes. |
 |
Can
compromises reinforcement detailing, particularly when used as planks
in bridgeworks. |
 |
Tolerances of panels and permanent works, creep during positioning. |
|
|
|
Attention |
To minimize demolition waste and provide maximum recycling
opportunities, the use of permanent formwork should be carefully
considered. Permanent formwork using different material types may be
difficult to recycle. |
|
|
|
|
|
|
Large
Panel Formwork |
|
|
|
|
|
Large panel
formwork consists mainly of large pieces of metal formwork. It is
most suitable for construction activities where formwork is highly
repetitive as it can be reused many times. Therefore, its design is
specified for the construction of the load bearing walls of typical
floors in high rise tower blocks. |
|
|
|
|
|
|
Compared with
traditional timber formwork, metal panel formwork has several
advantages. The use of large panel formwork can save time and labour
in erecting, striking and re-erecting the formwork as the panel is
handled as one unit. It can also produce a concrete surface, which
is neater than is produced normally by conventional timber formwork,
and the surface essentially needs no additional applied finishes for
levelling. On site waste audit records also show large panel
formwork systems are effective in reducing concrete waste generated
by losses due to damaged formwork, which usually accounts for 30% of
the total concrete waste. However, because of the weight of large
panel formwork, tower cranes should be available for its handling. |
|
|
|
|
|
|
|
|
|
|
Large panel formwork |
|
Removal of formwork |
|
|
|
|
|
|
Different
large panel formwork systems are widely used today by contractors
for constructing standardised housing blocks, and are broadly
classified as wall forms, table forms and tunnel forms. |
|
|
|
|
|
|
 |
Wall Forms |
|
|
|
|
|
|
The wall
forms are combined with the slab form so that the wall and slabs can
be formed monolithically in one casting operation, and the number of
joints between panels is minimised. There is less chance of grout
leakage or an uneven surface finish at the joint, which is a common
fault with in traditional timber formwork. |
|
|
|
|
|
|
 |
Table Forms |
|
|
|
|
|
|
Standard
modules of housing blocks are relatively large in span and large
table forms are widely used for assembly time reduction, fewer
joints and better surface finishes. The table method uses separate
vertical forms for walls and horizontal table forms for floor slabs.
The work is done in two stages. First, the walls are cast, and forms
are stripped, the tables are then positioned, and the horizontal
slabs are cast. |
|
|
|
|
|
|
 |
Tunnel Forms |
|
|
|
|
|
|
The half
tunnel is composed of vertical and horizontal panels set at right
angles and supported by struts and props. The walls and slabs are
cast in a single operation. Like the wall-forms and table forms,
this reduces not only the number of joints, but also the assembly
time. Therefore, the casting of walls and slabs can be completed in
the one day. |
|
|
|
|
|
|
Steel
Forms |
|
|
|
|
|
Because steel
forms are very durable, one set of steel forms can be used to
complete a project, and then reused for another project or scrapped
for recycling. Steel forms can produce a better quality concrete
finish when compared with timber forms. Although their initial cost
is higher, they can be cheaper in the long run, particularly with
their recycling potential. |
|
|
|
|
|
Composite
Steel Decking |
|
|
|
|
|
Steel
decking, becoming a permanent part of a composite slab, serves as
both the working platform and formwork for supporting the in-situ
slab concrete in the construction stage. The steel of the decking
can also utilised to provide some of the required permanent
reinforcement for the slab. In other words, the decking can replace
both timber formwork and bottom reinforcement, reducing the amount
of temporary works and formwork required. |
|
|
|
|
|
|
Aluminum
Forms |
|
|
|
|
|
Aluminum
formwork consists of small aluminum framed panels which are easy for
handling. It is fast to erect and strike and the floor cycle can be
4 days. It is durable and can be reused over 100 times. Although it
is more expensive than steel and timber, its merit is its
lightweight and recycling potential. |
|
|
|
|
|
|
Plastic
Forms |
|
|
|
|
|
PVC and
polyurethane forms can be used to replace timber forms in either
rigid or flexible formats. Special floor forms made of fibreglass
are occasionally used (6%). They can be reused over 50 times and
produce a concrete surface finish similar in appearance to fine
snake skin. If a smooth finish is desired, a paste wax or
water-based release agent can be applied to the form. |
|
|
|
|
|
|
 |
Rib Loc
Circular Column |
|
|
|
|
|
|
This UPVC
form is usually used to cast circular columns of diameter ranging
from 150 to 3000mm. It is made by spirally winding a ribbed plastic
profile into a tube. This enables column forms to be constructed
which are strong, lightweight, easy to strip and which provide an
excellent surface finish. The surface also incorporates the inherent
“waxiness” of extruded plastic and no form oil is required.
Square stabilisation timbers are fixed at the foot of the column
formwork to stop the formwork moving out of position. Vertical
bracing timbers are placed against possible movement while
concreting. The process is cost efficient with recycling potential. |
|
|
|
|
|
|
|
|
|
|
UPVC
column forms |
|
Erection
of column forms |
|
|
|
|
|
|
 |
Pecaform |
|
|
|
|
|
|
This is made
by laminating a layer of polyethylene to each side of a high tensile
steel wire mesh. This combination creates a material that is both
light and structurally strong, making it very easy to handle. It can
be used for constructing ground beams, pile caps, footings, curved
structures, ribbed and waffle slabs. The formwork is cut-to-size and
bent to shape at factory and arrives at site ready for installation.
There is no need to strip formwork after the concrete has cured. No
waste is produced. A clean and neat site can be obtained in the
foundation stage with Pecaform. |
|
|
|
|
|
|
|
|
|
Construction
of pile caps using Pecaform |
|
|
|
|
|
|
|
|
Backfill
around pile caps about 150mm from the top level of Pecaform |
|
|
|
|
|
High
Density Overlaid (HDO) Plywood |
|
|
|
|
|
The coating
of conventional plywood with a thick layer of polymer resin may
improve the quality and durability of the formwork. For example,
applying a medium density overlay or a high density overlay on
plywood can increase the number of reuses to 20. The form can be
easily dismantled and handled by small cranes and can be adjusted to
suit architectural requirements. |
|
|
|
|
|
|
Example
Supplier for Aluminium Formwork |
|
|
|
|
|
 |
VSL
Hong Kong Limited
|
|
3/F
Stelux House, 698 Prince Edward Road East, San Po Kong, Kowloon,
Hong Kong.
|
|
Tel:
(852) 2590 2288
|
|
Fax:
(852) 2590 0290
|
|
|
|
|
|
|
Example
Application for Steel Formwork |
|
|
|
|
|
 |
Cheung Sha Wan West Phase-II, Hong Kong
|
 |
Proposed
Redevelopment Oxford House at Quarry Bay, Hong Kong
|
 |
Proposed
Residential Development at 5-7 Blue Pool Road, Happy Valley,
Hong Kong
|
 |
Residential
Development at Aldrich Bay Reclamation, Shau Kei Wan, Hong
Kong
|
 |
Sau
Mau Ping Estate Redevelopment Phase-V, Hong Kong
|
 |
Shek
Yam Estate Phase-III, Hong Kong
|
 |
Tseung
Kwan O Area 73A Phase-II, Hong Kong
|
 |
Tseung
Kwan O Area 74 Phase-IV, Hong Kong
|
|
|
|
|
|
|
Example
Application for Aluminium Formwork |
|
|
|
|
|
|
|
|
|
|
|
Example
Application for UPVC Formwork |
|
|
|
|
|
|
|
|
|
|
|
|
|