Notable Features |
|
 |
Application of
steel formwork |
 |
Application of
UPVC formwork |
 |
Application of
Timber formwork |
 |
On-site
sorting of waste |
 |
Reuse
of steel hoarding |
Basic
Information |
|
 |
Location: Happy
Valley |
 |
Building Type: Residential |
 |
Contract Period:
494 days |
 |
Gross
Floor Area: 13,900m2 |
 |
Client:
Dorfit Properties Ltd. |
 |
Architect: Chung
Wah Nan Architects Ltd. |
 |
Structural Engineer:
Harris & Sutherland Consulting Engineers |
 |
E&M
Consultant: Parsons Brinckerhoff (Asia) Ltd. |
 |
Quantity Surveyor: Levett
& Bailey Chartered Quantity Surveyors |
 |
Main Contractor: Hsin
Chong Construction (Asia) Ltd. |
 |
Contract Sum: Approx.
HK$ 210 million |
|
|
![]() |
|
Steel
Formwork |
|
Steel
formwork was used for the circular columns with diameter larger
than 1 metre to maintain a more rigid formwork for concreting.
As the building is in the shape of an ellipse, steel formwork
was also adopted to construct the edge beams at the frontage of
the typical floors such that a better quality of curved
surface could be formed. In order to achieve a 5 day floor
cycle, the steel formwork for the edge beams were of handy
type since the tower crane had been fully occupied for loading
material and concreting. The steel formwork was scrapped
for sale after completion. |
|
|
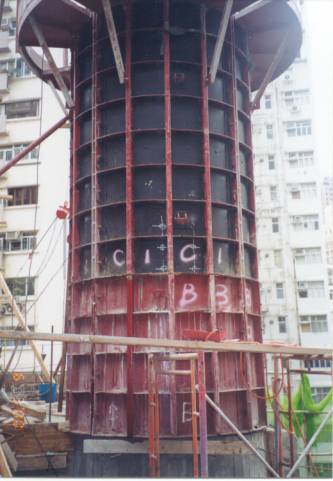
|
|

|
UPVC Formwork |
|
UPVC formwork was used for
circular columns with diameter of about 1 metre. High strength
concrete was adopted for podium floor. Since the UPVC formwork could
not
be reused after striking, there was no need to hurry with striking
the formwork for the next floor, the high strength concrete could be
kept in the formwork for curing for 5 days.
|
|
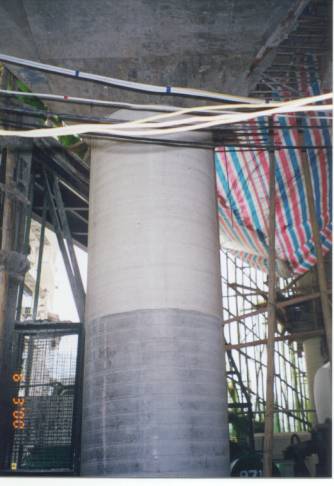
|
|

|
Timber Formwork |
|
Timber formwork was used for
constructing the non-typical area and the floor slab.
|
|
|
Contact
of Contractor
|
|
Hsin Chong Construction (Asia)
Ltd.
|
Hsin Chong Center, 107-109 Wai
Yip
|
Street, Kwun Tong, Kowloon
|
Tel:
(852) 2579 8238
|
Fax:
(852) 2516 9430
|
|

|
|