Notable Features |
|
 |
Construction waste
reduction/recycling program |
 |
Reduced
construction waste due
to use of factory manufactured precast concrete elements |
 |
Application of
large panel steel formwork |
 |
Use of drywall for
the internal partitions |
 |
Use of
semi-precast slab |
 |
Use of precast facade |
 |
Use of precast
staircase |
 |
Use of tubular
scaffolding |
 |
Use of spray plastering |
 |
Use of gondola to
apply external finishes |
 |
Reuse of steel
safety guard |
 |
Reuse of steel
hoarding |
Basic
Information |
|
 |
Location: Tseung
Kwan O Area 74 |
 |
Building Type: Residential |
 |
Contract Period:
December 98 – December 2000 |
 |
Client: The Hong
Kong Housing Authority |
 |
Main Contractor: Dragages
at Travaux Publics |
 |
Contract Sum: HK$
1,100 million |
Overview |
|
The
Tseung Kwan O Area 74 Phase 4 was a residential building project and
the following major items were executed under this contract: |
|
 |
Six
40 storeys Concord Blocks (Option 1) |
 |
One
7 storeys carport |
|
Associated external works
|
|
|
|
Plastering and Finishing
|
|
|
|
The
speed of applying spray plaster is faster than
traditional cement sand plaster. Although the cost of
spray plastering is double as much as traditional
plastering, it is considered as defective free product
which provide a very smooth and accurate surface. |
|
|
|
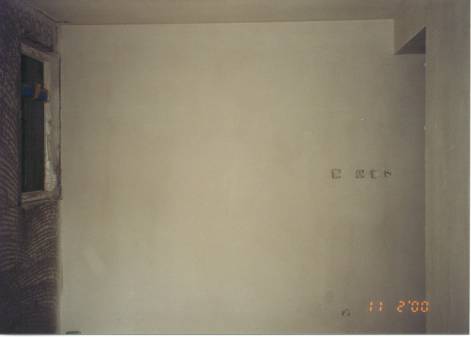 |
|
|
|
Gondola
was used to apply external finishes. |
|
|
|
|
|
|
|

|
|
Waste Management |
|
|
|
 |
Source
Separation |
|
|
|
Source
Separation was considered to be more feasible than Centralized
Separation. The waste was separated at the respective floors
and then transported through refuse chute to the ground floor
at appointed time. In this case, situation of half-full skip
might be occurred. However, there was problem to install another refuse
chute (one for inert waste and one for non-inert waste) due to
the ground floor had been fully occupied with materials such
as reinforced bars, precast elements, etc. |
|
|
|
|
|
|
|
There
was no extra space for another outlet for refuse chute. In
addition, installation of extra refuse chute inside the
building required extra opening on each floor. |
|
|
|
 |
Material
Control |
|
|
|
The subcontractors were
generally required to supply both material and labour so that
they would reduce the wastage of material as possible as they
could.
|
|
|
|
For
the materials such as instant mortar, dry wall and grano
provided by the main contractor, a mock up flat was
completed first and this served as a control for other flats.
The material wastage was generally 3%. |
|
|
|
 |
Reusable
materials |
|
|
|
The
steel hoarding was reused. |
|
|
|
Steel
tubular scaffolding was used to construct the carport. This
saved the waste of bamboo scaffolding. However, the cost of
tubular scaffolding is normally three times the cost of bamboo
scaffolding. For this site, the subcontractor agreed to supply
and install tubular scaffolding at 50% higher for promotion |
|
|
|
At each opening of lift
shaft, reusable steel safety guard instead of timber boarding
was used. This reduced timber waste.
|
|
|
|
|
|
|
|
At
each staircase, steel tubes and chains were used as safety
guard. This also reduced timber waste. |
|
|
|
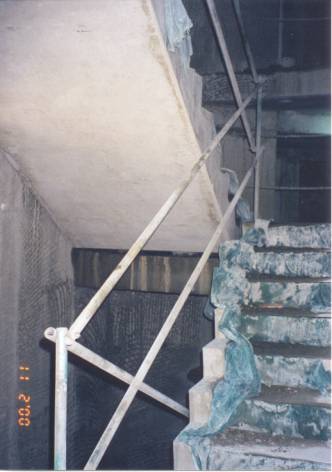 |
|
|
|

|
|
Contact
of Contractor
|
|
|
|
Dragages
at Travaux Publics (HK)
Ltd. |
|
11/F, Island Place Tower, 510
King's Road |
|
North Point, Hong Kong
|
|
Tel:
(852) 2511 4261
|
|
Fax:
(852) 2588 1979
|
|
|
|

|
|
|
|
![]() |
|
Wall System |
|
The Housing
Authority specified to use large panel steel formwork for the
construction of load-bearing walls. This saved time in
erecting, striking and re-erecting the timber formwork as the
steel formwork is handled as one unit. One set of formwork
could
be repetitively used throughout the block. |
|
|
|
However, it
took 6 days to complete one floor for the tower crane was fully loaded to transport materials. With traditional
timber formwork, a 4 day floor cycle could be achieved. Besides,
the cost of steel formwork was 25% higher than the cost of
timber formwork.
|
|
|

|
Dry Wall |
|
‘Ytong’
dry wall system was used to form the partitions of the flat. Ytong
Autoclaved Aerated Concrete (AAC) is manufactured from sand, lime,
PFA, cement, water and aluminum powder. It is composed of calcium
silicate hydrates and many small pores. The accuracy of Ytong size
can easily be controlled because the size of the product will not
vary after casting. Also, the shrinkage of Ytong product is small
which is only up to 0.055%. In addition, this product is very light
– the density of which ranges from 400-700kg/m. It can be cut into
different size according to dimension requirement by simple
equipment such as hand saw or electric cutter. |
|
|
|
It
has the advantage of easy assembly or disassembly to give a flexible
layout to the flat without any concreting process which will produce
waste. |
|
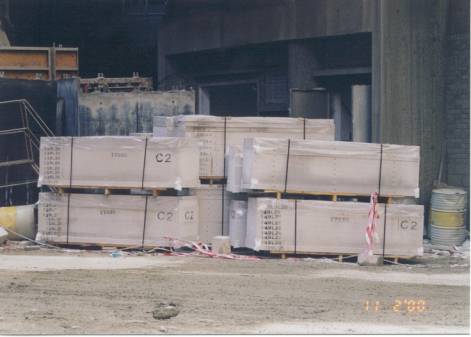 |
|

|
Slab
System |
|
Semi-precast slab was adopted to
be the slab of each floor. 70mm thick precast slab was used to serve
as the formwork for the 80mm in-situ concrete layer, thus forming a
150mm thick concrete floor. This saved the time in erecting and
striking the timber formwork as well as forming a smooth ceiling
finishes for the floor below.
|
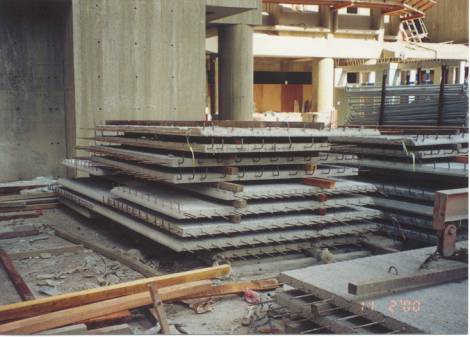
|
|
However, the
precast slab must be handled and transported with care to
prevent cracking of the slab. |
|
|

|
Precast
Facade |
|
The
precast facade was off-site prefabricated and transported to the
site. It was stored at the ground level and was hanged to the required
floor by tower crane. |
|
|
|
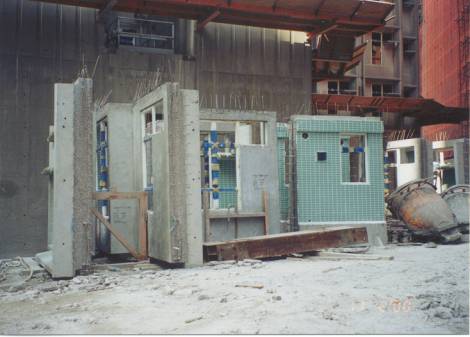 |
|
It
is cost effective to use precast facade in mass production. |

|
Precast
Staircase |
|
Another
feature is the precast staircase which was constructed in 8 risers. |
|
|
|

|
Tubular
Scaffolding |
|
Tubular
scaffolding was used for constructing the carport |
|
|
|
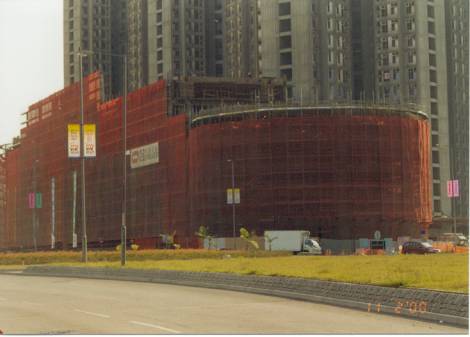
|
|

|
|