Notable Features |
|
 |
Application of
“Ventonit” sprayed
plaster |
 |
ISO
14000 certification |
 |
On-site
sorting of waste |
 |
Reuse of steel
hoarding |
 |
Reuse of
large timber panels |
 |
Recycled
waste water |
Basic
Information |
|
 |
Location: San
Po Kong |
 |
Building Type: Residential |
 |
Contract Period:
July 1998 to Jan 2001 |
 |
Gross
Floor Area: 179,100m2 (domestic), 9882m2 (non-domestic) |
 |
Client:
City Team Development Limited |
 |
Architect: Chows
Architects Limited |
 |
Structural Engineer:
Fugro (H.K.) Limited |
 |
E&M
Consultant: Carnival Consultant Limited |
 |
Main Contractor: Hip
Hing Construction Co., Ltd |
 |
Contract Sum: HK$1,300
million |
Overview |
|
The following major items were
executed under this contract: |
|
 |
Demolition
of barracks including 12 existing buildings |
 |
Foundation,
Site Formation Works, Construction of 12 nos. of residential
blocks, 1 carport block with shops, 1 elderly centre, 2
footbridge connections, and landscape gardens. |
|
|
|
|
|
The
demolition work was carried out by Hip Hing and commenced on
31 July 1998. There was no requirement for separation of
waste. On-site sorting of demolition waste was partially
executed. These materials included steel gates, windows,
reinforcement, which could be resold in the market for money.
Asbestos was also demolished separately according to the
building regulations. The rubble and other wastes were disposed
to the landfill. As for external works, some trees were
required to be preserved in the contract. |
|
|
|
|
The
project mainly involved the construction of 12 towers of
residential blocks, a carport block with shops and an elderly
centre. Seven towers are 22 storeys and five towers are 30
storeys high. Traditional methods were adopted for this
project as the profile of the facades involved construction of
A/C hoods, which was not suitable to use steel form. |
|
|
Spray
Plastering |
|
The
low-waste technology, used for this project was “Ventonit”
sprayed plaster. For the wall surface, cement sand bedding was
applied prior to the application of sprayed plaster. As for the
ceiling surface, sprayed plaster was directly applied to the
concrete surface. The labour cost of sprayed plaster was HK$53
per square metre and the material cost was HK$27 square metre,
as at December 1999 prices. The cost of sprayed plaster is about
30% higher than traditional cement sand plastering. The
advantage of sprayed plaster is the guarantee of speed and
quality. It is getting popular in Hong Kong.
|
|
|
Contact
of Contractor
|
|
Hip
Hing Construction Co., Ltd. |
29/F,
New World Tower, 16-18 Queen's |
Road
Central, Hong Kong |
Tel:
(852) 2525 9251
|
Fax:
(852) 2845 9295
|
|

|
|
|
|
![]() |
|
Waste Management |
|
 |
Waste
Management Plan |
|
|
For
the purpose of identifying opportunities and achieving
continual improvement on environmental performance through a
systematic approach, Hip Hing Construction Co., Ltd. has
documented and maintained an Environmental Management System
(EMS) conforming to ISO 14001:96 requirements. They have
obtained the ISO 14,000 certificate. Issues related to waste
management such as segregation of good and reusable material
as well as avoidance of unnecessary wastage resources are also
included in the EMS manual. |
|
 |
On-site
sorting of waste |
|
|
On-site
sorting was partially performed. Chemical waste was stored
separately as required by regulations. Large rotten timber
panels and surplus reinforcement were transferred to the ground
floor by tower crane. There was 1 no. of plastic refuse chute
for each block. Although plastic refuse chute can reduce
noise, it is not durable. There was no separation of papers,
cans, lunch boxes, plastic conduits and rubble, etc. |
|
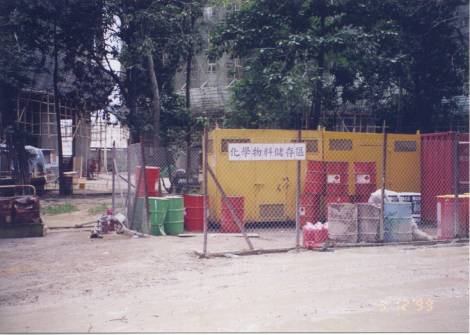
|
|
The
problems associated with separation of waste on site are the
extra resource and labour required as well as educating the
labourers. If on-site sorting of waste was to be carried out,
it was preferred to be sub-let to the subcontractor and to be
conducted centrally since space was available in the site.
|
|

|
|
 |
Material
Control |
|
|
The
wastage was generally below 5%. The subcontractors were
generally required to supply both material and labour so that
they reduced the wastage of material as possible as they could.
In addition, a mock up floor/flat was used to control the use
of material for the remaining typical floors. |
|
 |
Use
of recycled materials |
|
|
 |
Waste
water was discharged to the waste water treatment plant
and then the treated water was distributed to the automatic tire
washer. |
|
|
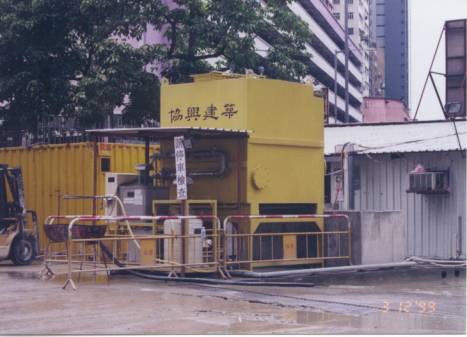 |
|
 |
Reusable
materials
|
|
|
 |
The steel hoarding
was used for the demolition contract as well as the
building contract. |

|
Large
timber panel was reused for working platform, etc. |
|
|

|
|